Research Laboratory at Deakin University - Waurn Ponds
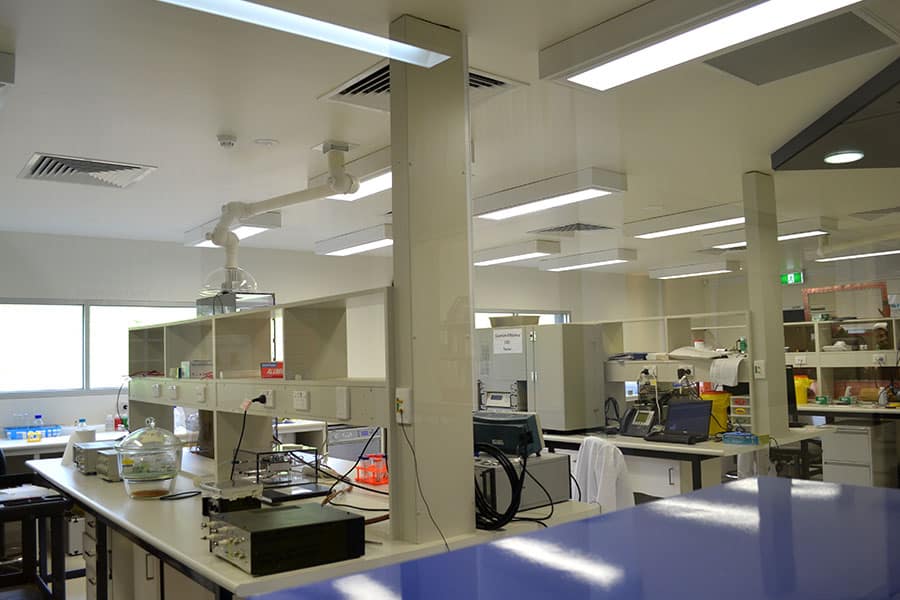

Client: Deakin University
Project: ND Building Laboratory at Waurn Ponds Campus
Scope: Major refit of ND building for specialised laboratory application.
Delivered: July 2012
Value: circa $1,300,000
Key Trades: Hydraulic, Electrical, Mechanical, AV, Data, Security, Finishing, Joinery.

2012 evolved to be the year Loaram became expert in the configuration of specialised laboratories.
Building ND started life as a covered shearing platform on the original rural perimeter of the Deakin Waurn Ponds Campus. Over time the space has been converted and enclosed as the area evolved into the technology precinct for this campus.
The ND project tasked Loaram with the responsibility of converting the internally open plan space (previously enclosed in past projects) to a state of the art research laboratory. A new mezzanine level was created, in part to accommodate the complex mechanical systems and BMS that alone reflected a $400K investment.
As a lab, many specialised technologies became the responsibility of Loaram to deliver. This included a gas detection and alarm system, fire detection system, EWIS, full access control & security interface, new communications capacity including new communications room with rack and all associated works to KRONE 20/20 certification. Existing fume cupboards were supplemented with new, and a complex deionised water treatment plant was procured from Europe especially for the application.
Structurally, the existing site threw up many challenges. Major floor levelling was required to correct previous falls for a redundant drainage design. Core services were found incapable of servicing the new application, meaning significant works bringing in new services with associated approvals, trenching, chasing, new underground conduits and pits plus extensive out of hours shut down works to bring the site on line.
The extent of the new plant introduced a detailed roof access design and a package of custom fabricated security cages to ensure the new plant stayed in place! The fabric of the building was upgraded with new cladding, soffit lining, storm water drainage and external civil works including managing an previously undetected existing underground storage tank.
The project wrapped up with a detailed finishing package including a $100K joinery scope of chemical resistant laminates and custom fabricated steel framed work benches. The same chemical resistant theme extended to the floor and wall finishing package.
The project was completed to original program even after absorbing numerous additional works as the site revealed many unknown challenges.
Project Reference: Steven Skratulja – Project Manager – 0407 459 676
